Forging
Forging - metal shaping by plastic deformation, spans a myriad of equipment and techniques. Though forging is a matured technology, it has its Cost Advantages. Precision forging normally means close-to-final form or close-tolerance forging. It is not a special technology, but a refinement of existing techniques to a point where the forged part can be used with little or no subsequent machining. Improvements cover not only the forging method itself but also preheating, descaling, lubrication and temperature control practices.
The decision to apply precision forging techniques depends on the relative economics of additional operations and tooling versus elimination or reduction of machining effort and material wastage. Because of higher tooling and development costs, precision forging is usually limited to high-quality applications or medium to high volume production.
Gem-Metal is able to offer you the benefits of forging which are listed below:
Key Benefits
- Less raw material wastage. It has been proven that forging combined with high precision machining could reduce material wastage by as much as 50%.
- Less machining time needed for high precision finish (up to 50% machining time saved).
- Better product tensile strength can be achieved through forging than pure machining.
- Shorter product manufacturing cycle time - hence faster Time-To-Market (TTM).
Capabilities
The company is able to provide both hot and cold forgings depending on the parts requirement.
Hot Forging
Hot forging is used for the deformation of metal that features a high formability ratio. Other considerations for hot forging include:
- Production of discrete parts
- Low to medium accuracy
- Scale Formation
- Low stresses or low work hardening
- Homogenized grain structure
- Increased ductility
- Elimination of chemical incongruities
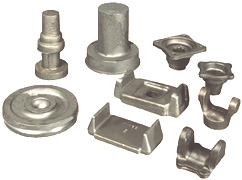
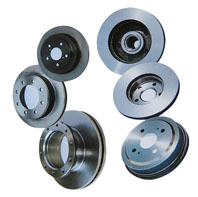

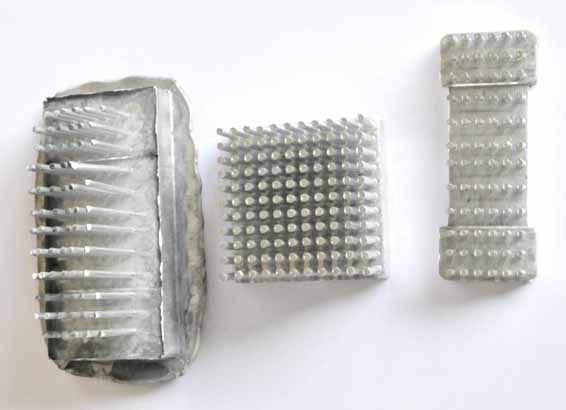

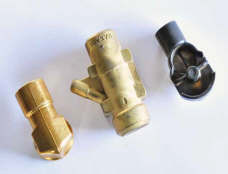
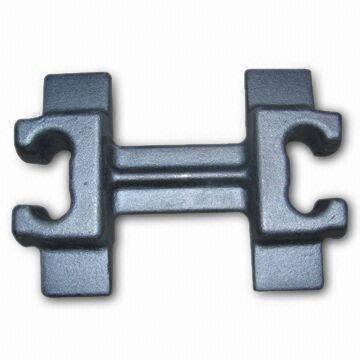
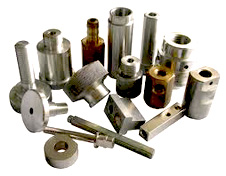
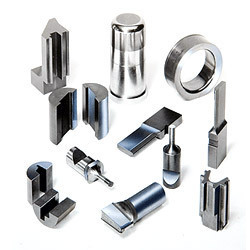
Cold Forging
Hot forging is used for the deformation of metal that features a high formability ratio. Other considerations for hot forging include:
- Easier to impart directional properties
- Improved interchangeability
- Improved reproducibility
- Increased dimensional control
- Handles high stress and high die loads
- Produces net shape or near-net shape parts
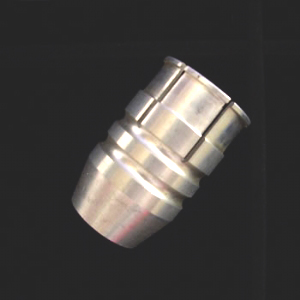
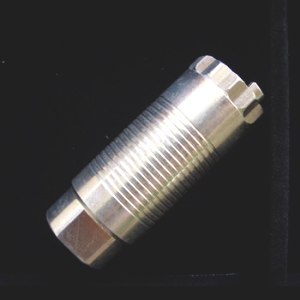
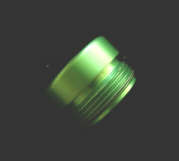
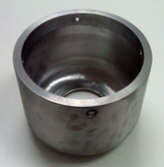
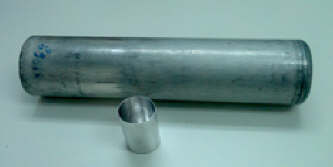
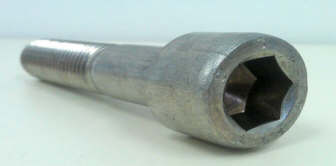
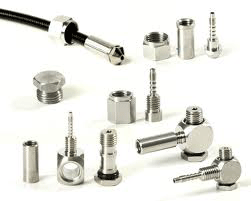
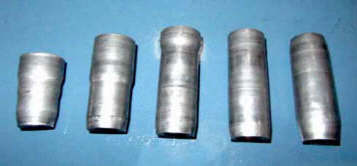